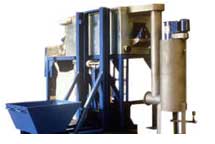 The
use of an HEI sludge dryer provides up to a 4 to 1 reduction of sludge
volume. This results in a dramatic reduction of sludge disposal and
handling costs and provides a rapid payback period. HEI manufactures
batch process, as well as continuous process sludge dryers. The batch
process dryers use steam, gas, or electric heat sources, while the
continuous process dryers use either steam or gas.
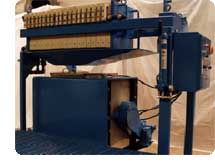
Filter Press over 4 cu. ft. Batch Sludge Dryer |
|
The HEI batch dehydration system is designed to meet the stringent environmental requirements for thermal extraction equipment.
The design flexibility of the HEI batch dehydrator allows the
system to be positioned directly beneath the filtration equipment
whenever possible to save material handling.
In cases where wet or dried material must be transported, HEI offers a complete line of material handling equipment.
The dehydration process is accomplished by externally heating the
dehydration chamber with steam, gas, or electric heat and carefully
controlling the internal dehydration temperatures and the dehydration
steam exhaust.
Additionally, many wastes can be batch treated that are environmentally objectionable in a continuous dehydration system.
General operation of the HEI batch dehydration system consists of
dropping a controlled amount of material through the dehydration
chamber door. The process timer is set to the required dehydration
time. A custom fabricated steel blender ribbon continuously turns the
material exposing all surfaces for dehydration.
|
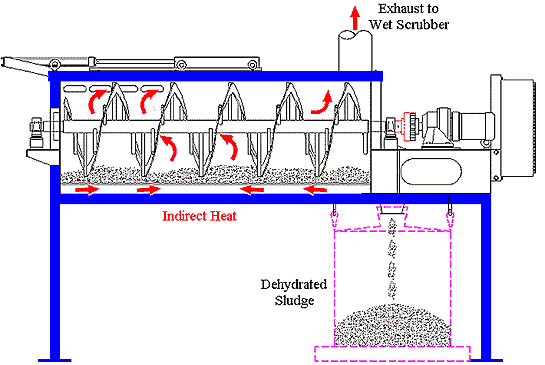
When the preset dehydration time (typical cycle is 5 to 6 hours)
has elapsed, the unit automatically shuts down. At this time, the
operator switches to the discharge cycle to allow automatic emptying of
the machine.
HEI batch process dryers are available in various configurations and range in capacity from 4 cu. ft. to 100 cu. ft.
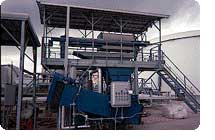
Filter Press over Steam Heated Continuous Process Sludge Dryer with Explosion Proof Control Panel |
|
The HEI continuous dehydration system is engineered to meet the
state of the art technology required for the future of waste
minimization. At the same time ease of maintenance, control modularity
and flexibility have been maintained.
The design flexibility of the HEI continuous process dehydration
system allows the system to be positioned directly beneath the
filtration equipment whenever possible, in order to reduce material
handling labor.
In cases where wet or dried material must be transported, HEI offers a complete line of material handling equipment.
The HEI indirect heat continuous process dehydration systems are
available in models with process capacities from 3 to 20 cu. ft./hour.
General operation of the HEI system starts by dropping the
material to be processed into the infeed blender. The drive system,
turning the blender mechanisms, as well as the infeed auger, meters the
material at an adjustable rate into the dehydration chamber(s). The
material is subjected to indirect heat and discharged from the chamber
in a dry aggregate similar to oil dry or freeze dried coffee. In
special applications, the process material can be discharged in a finer
consistency.
|
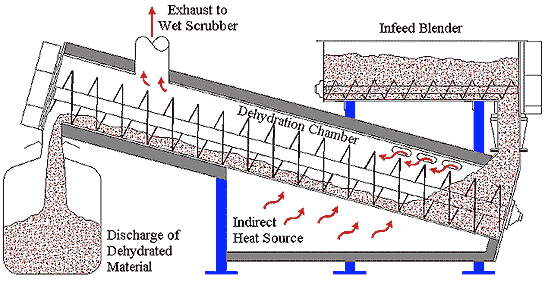
The drying process is accomplished by indirectly heating the
insulated hot air chamber with steam or gas. Heat is transferred
through the walls of the process chamber and into the material in
process. This system allows for a totally indirect heated dehydration
unit. Combustion gasses flow through a special manifold injection
system into the process chamber to insure optimum efficiency.
The control of the continuous process is accomplished by means of
a variable speed drive to meter the material from the hopper, and a
second variable speed drive to convey the flow of material through the
drying process.
|