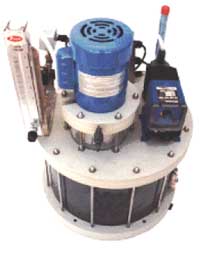
- SELF CONTAINED AGING CHAMBER
- REDUCE POLYMER CONSUMPTION
- LOW MAINTENANCE
- FULLY AUTOMATED
- 30 DAY UNCONDITIONAL WARRANTY - 1 YEAR PARTS
|
||||||||||||||||||||||||||||||||||||||||||||||||||||||||||||||
![]() - SELF CONTAINED AGING CHAMBER - REDUCE POLYMER CONSUMPTION - LOW MAINTENANCE - FULLY AUTOMATED - 30 DAY UNCONDITIONAL WARRANTY - 1 YEAR PARTS
The Patented Polymixer unit thoroughly
dilutes and ages emulsion polymers into a fully activated and uniformly
diluted polymer solution. Pressurized water and small quantities of
concentrated polymer are blended together within an in-line mixing
chamber. The mixing unit contains a perforated turbine style impeller
driven by a direct drive heavy duty motor and is baffled to produce
high energy mixing of G-10,000 sec-1 throughout the entire mixing
chamber eliminating channeling and vortexing. Even high viscosity
polymer may be rapidly blended in the high energy mixing chamber
producing a consistent flow of homogeneous diluted polymer, free of
"strings" and "fish eyes". The mixing chamber is constructed of
transparent plastic with the entire mixing process readily visible to
the operator.
The diluted molecules of polymer then pass through a Patented Aging Chamber
which provides polymer adequate time to hydrate into highly active long
chains of polymer. Since the fragile polymer molecules' integrity is
maintained, the activity level attained is far superior to diluted
polymer solutions produced in non-aged polymer blending devices.
High shear mixing together with the Polymixer's
patented aging chamber completely activates polymer to significantly
reduce polymer consumption. The mixing chamber subjects emulsion
polymers to an ultrahigh shear zone (G=10,000 sec-1 for up to 30
seconds) to mechanically strip the polymer of oil, uniformly disperse
and prevent agglomeration; leaving microscopic particles (near
molecular in size) of polymer to hydrate. The 15 gallon patented aging
chamber mounted beneath the mixing chamber provides polymer sufficient
aging time (up to 10 minutes) to hydrate into long chains of highly
active polymer.
![]()
A recent independent test conducted on polymer
aging exhibits a significant improvement in the percentage of activity
created by increasing the aging time of polymer. A comparison was made
using two competitive polymer mixing units without aging and the HEI
Polymixer which has a 10 minute aging time. The same metering pump on
the same setting was used in the test. Conductivity readings are in
microSiemens. The above graph details the test results.
The blue area represents the conductivity of the
dilution water. The total bar chart, blue plus red, represents total
conductivity at the exit of the polymer mixing device. Activation
efficiency can be determined by the following test.
Activation Test: [(CT1-C1) ÷ (CT2-C1)] X 100 = __________% Activity.
Competition [(330-300) ÷ (500-300)] X 100 = 15% HEI Polymixer [(515 - 300) ÷ (525 - 300)] X 100 = 96% Where C1 = conductivity of feed water, CT1 = conductivity at discharge of unit, and CT2 = conductivity after 1 hour of aging. The competitor's unit without an aging chamber
provided only 15% of the available activity of the polymer discharge.
(Note: Since the competitive models do not have high turbulent mixing
chambers, the emulsion polymer particles are not adequately "wetted"
and then even after an hour of aging time, the polymer reaches only 60%
of full activation.) The HEI unit developed 96% of the available
activity, registering conductivity of 515 microSiemens. Since the HEI
Polymixer produces an activated polymer having up to 5 times the
activity rate of the competitive model, it is readily apparent that for
equivalent results, the polymer consumption with an HEI system will be substantially less.
If you spend $800 per month on polymer, a 50% reduction of polymer
usage would cover the cost of replacing your ineffective system in less
than one year.
ACTUAL FIELD REPORTS VERIFY SAVINGS ON POLYMER USAGE RANGING FROM 20% TO 50%.
AGING DOES MAKE THE DIFFERENCE
Commonly failed parts contained in competitive polymer feeders such as belts and side-loaded bearings do not exist with the Polymixer.
The mixer motor is connected to the impeller via a stainless steel
direct shaft drive. All components that make-up the unit have been
engineered to be readily accessible. The operator can easily access any
Polymixer component within minutes.
Eliminate time-consuming, inconsistent batches of
wasted polymer. The Polymixer automatically and continuously blends
concentrations of emulsion polymer with pressurized water. Either low
water pressure or a power loss will shut the unit off automatically.
DIMENSIONS: 24" dia, 32" tall, 180 lb. empty 300 lb. service weight.
MATERIALS: Mixer motor is a 3/4 HP TEFC direct drive continuous duty, 1725 rpm operation (110 VAC, 60 HZ, 11 amps). Mixing chamber
is constructed of clear Plexiglas with four stainless steel baffles,
enclosing a stainless steel impeller mounted to a stainless steel
shaft. A ceramic/Buna-n mechanical seal is used. Aging chamber is constructed of PVC and polypropylene. Internal chambers are also PVC.
INPUT/OUTPUT FITTINGS: Input 1/2" FNPT for 100 gph/300 gph, 1" FNPT for 10 gpm/20 gpm. Output 1" FNPT.
MAX WATER PRESSURE: 100 psig, 30 psig minimum.
ELECTRICAL: 100 VAC, 60 HZ, max 15 amps, single phase service, 3-prong grounded plug.
|
||||||||||||||||||||||||||||||||||||||||||||||||||||||||||||||
![]() |
![]() |