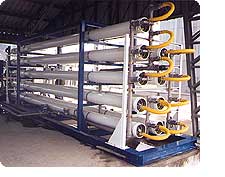
|
||||||||||
![]()
Reverse Osmosis is a process for removing
dissolved mineral salts, organic molecules and certain other impurities
by forcing water under pressure to pass through a semi-permeable
membrane.
HEI industrial Reverse Osmosis systems are
appropriate for applications with flow rates up to a standard size of
500 gpm per module, with modules being combined to provide even larger
flow rates. Single-Pass Reverse Osmosis units are ideal for most
situations, but Double-Pass Reverse Osmosis units can be provided for
those situations where ultra-pure water is necessary.
The Reverse Osmosis process reverses the natural
osmotic effect in which fluids with a low concentration of dissolved
solids pass through a membrane into an area of higher concentration.
With Reverse Osmosis, water is made to pass from a state of high
concentration to a state of low concentration.
Since Reverse Osmosis does not occur naturally, it
must be created by applying pressure to the high solids water in order
to force it through the membrane, with pressures from 200 to 400 psig
in most applications, 1,000 or even 1,200 psig for sea water
desalination and high solids conditions.
The pressure applied to the feed side of the RO
membrane must be much higher than the natural osmotic pressure of the
water in order for the osmotic process to be reversed. High pressure
pumps are used to create the pressure needed to produce economically
acceptable flow rates.
![]() The product flow of an RO is mainly a function of
temperature and pressure. System recovery (product divided by feed) is
limited by the characteristics of the feed water and can be controlled
through the use of recycle stream. Product quality is based on a
percentage of dissolved solids fed to the membrane. There should be an
economic balance between product quality and system recovery. High
recoveries increase concentration of dissolved solids in the system
which degrades quality, but high recoveries make the system more
efficient and decrease waste.
RO units do not deliver to service all of the
water that is fed to them. During operation, some of the incoming water
is used to wash down the membrane, and only part becomes finished
product water. Purified water is referred to as product and wastewater
is referred to as concentrate, or reject. The percent of water
delivered as product is called the recovery, and depends upon the
membrane and on total RO unit design considerations.
RO units are volume rated at 77°F (25°C) incoming
water temperature. Adjustments must be made if the incoming water
temperature varies.
HEI can provide pretreatment of water prior to the
RO process if it is required. Chlorine removal is important but high
hardness minerals should also be controlled by a softener or other
suitable methods of treatment. Hard water scale build-up impairs RO
unit performance. Turbidity, pH, iron, and other impurities must be
controlled for optimum RO performance.
HEI can provide ozone, ultra-violet and chlorination systems for potable water systems.
![]()
HEI builds physical, chemical and biological waste
systems to address treatment of the reject (concentrate), a concern
often overlooked in process design.
This study involves a Double Pass RO system for
high quality turbine engine NOx suppression water at an electricity
generating plant. They saved $500,000 capital costs over a resin
system, and approximately $100,000 yearly in operating costs. The
system is supplying at 75% recovery.
The following photograph shows the major
components of the installed system. From the left can be seen a) the
membranes, b) local control panel, c) 2 upright pumps, d) filter.
Behind is seen the panel room. Not shown but included in this
installation is a carbon filter. |
||||||||||
![]() |
![]() |