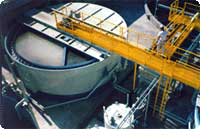 Hoffland
Environmental, Inc. (HEI) dissolved air flotation systems (DAF)
efficiently separate total suspended solids (TSS) and fats, oils, and
grease (FOG) particles from industrial effluents. The system generates
air bubbles ranging from molecular to micro bubbles. Air is dissolved
in the treated water by the addition of compressed air to a pressurized
stream of recycled effluent. The pressurized water then passes through
a pressure relief valve reducing the pressure to atmospheric. This
depressurized water is then mixed with the conditioned influent. When
the pressure is reduced the super-saturated air begins to precipitate
from solution. The molecules of air affix themselves or seed to the
flocculated solids. The precipitated molecules coalesce into a micro
bubble. The bubble with the suspended solids and/or minute oil droplets
are buoyant and float to the surface. This simple process combined with
optimum conditioning chemistry and properly designed equipment provides
a sophisticated solids and FOG separation system.
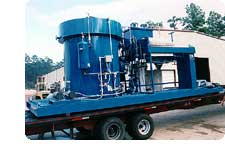 HEI
has performed extensive laboratory evaluation on the size of the air
bubble and effective liquid-solid separation. The data overwhelming
demonstrate that the smaller the air bubble, the more efficient the
separation. By comparison, the effluent from an induced air flotation
system (IAF) typically contains twice as much TSS and FOG as the
effluent from a DAF. In the few applications where the reduced
separation of the IAF is satisfactory, HEI is able to provide induced
air flotation as an alternative.
Besides dissolving air into recycle water, HEI’s
air dissolve tank also separates and vents excessive macro bubbles from
the system subsequently preventing surface disturbance in the DAF tank.
Only the pressurized water saturated with dissolved air, not bubbles,
is permitted to be commingled with the treated wastewater. Samples from
the air dissolve tank have a milky appearance from the microscopic
bubble. This HEI dissolved air system is much more effective than an
induced air system.
There are five important factors to be considered in properly sizing your DAF.
Air to Solids Ratio
is the quantity of air required to float a given amount of solids and
FOG’s. It usually is expressed as lbs. of air/lb. of solids with the
normal ration being between 0.01 and 0.10 lbs air/lb solids. HEI
recommends a 0.03 ratio. The amount of air that dissolves in water is
determined by the temperature of the recycled water and imposed
pressure. Under normal HEI design conditions (75 psig at 70°F) the
average amount of air dissolved is 9% by weight. The TSS (total
suspended solids) must be analyzed and the appropriate percent recycle
rate established. A waste stream of 1000 mg/l TSS will require a
recycle rate of 50%, and 2000 mg/l TSS will require 100% recycle.
Hydraulic Loading (gpm/ft2) is the
relationship between available surface area of the flotation cell and
the total flow rate through the DAF influent plus recycle. Hydraulic
loading is total flow rate divided by the effective surface separation
area. Design hydraulic loading varies from 1.5 to 5.0 gpm/ft2. HEI
recommends 2.5 gpm/ft2.
Launder Weir Ring Overflow Rate in gpm per
linear foot is a convenient-to-calculate value that can be assumed to
reflect eddy current formation that would carry solids or FOG under the
underflow baffle. It must not be so rapid as to entrain precipitated
solids. The overflow must be completely uniform across the launder weir
(and thus under the baffle).
HEI prefers the circular DAF design to reduce the
launder weir overflow rate. The DAF influent enters through a central
mixing well ("distributor") and flow out horizontally through ports.
The bubbles attached to the TSS and FOG float to the surface. The
cleaned water flows down under a baffle and over the launder weir. This
radical outflow design dramatically reduces internal velocity and eddy
currents, which assures complete separation of the buoyant flocculated
particles.
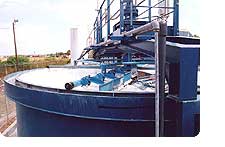 HEI
does not normally recommend the rectangular designed DAF unit because
the high velocity at the inlet is never reduced. Hence, the expected
separation is not as efficient in the rectangular design as can be
expected in the circular design DAF’s. HEI utilizes the rectangular
design for customers with limited available space.
Solids Loading is the relationship between
the effective surface area of the DAF cell and the total amount of TSS
& FOG entering the system. The average design load is 1.0 to 3.5
lbs./hr/sq. ft. HEI recommends not exceeding 2.0 lb./hr/sq. ft. The
calculation should include not only the influent TSS but also all
chemicals added to condition and flocculate the waste stream.
Solids Removal of both float and sediment
(if any) must also be considered in the general design. In addition to
the skimming rake to remove the float, HEI also has a bottom rake to
sweep any sediment to the center bottom outlet.
HEI dissolved air flotation systems are very
effective in the removal of suspended solids and free FOG. Emulsified
oil and grease must be chemically conditioned before removal. Due to
"van der Waals" charges, particles in industrial wastewater usually
exist as a colloidal suspension. These charges must be neutralized
before the solids can be flocculated and floated. The small,
destabilized colloids collect and agglomerate with the long chained
polyelectrolyte into large floccules which can be rapidly floated to
the surface.
|
The conditioned and flocculated influent is
conveyed to the center distribution well through a large mixing tube
(1). The pressurized recycle water saturated with air is added to the
treated water through HEI’s proprietary mixing nozzle which induces
mild turbulence throughout the mixing tube (2). The pressure of the
recycle water is reduced to atmospheric at the pressure control valve
(9). HEI's mixing nozzle uniformly blends the air saturated recycled
water with the conditioned influent as the dissolved air precipitates
from solution.
Central Mixing/Distribution |
The depressurized recycle water with the
conditioned influent flows into the central distribution/mixing well
(3). The distribution chamber is designed to retain the mixture and
provide gentle hydraulically mixing for a short commingling period.
Adequate time is permitted for the precipitated air molecules to seed
the suspended solids and agglomerate to produce buoyancy. Other
micro-bubbles get trapped inside the pores of the flocs, which
certainly would not happen with larger bubbles. The wastewater flows
out near the top of the mixing well through distribution orifices to
uniformly distribute the treated water throughout the DAF cell.
Float Removal and Sediment Removal |
Heavy solids, if any, settle on the bottom of the
DAF tank. A bottom rake drive (4) prohibits solids from rat-holing
(which is a common problem with cone-bottom tanks without rakes) by
continually moving the collected solids to a center outlet. Heavy
solids removal is controlled by valve #12 and may be either
automatically or manually initiated. A surface skimmer moves the
buoyant solids that float over a beach weir (5). The float then slides
down the inclined floor of the trough to the outside collection tank
(10).
The flow rate dramatically slows as it radically
moves from the center of the DAF cell to its circumference. Adequate
time is provided for the buoyant suspended solids to rise to the
surface, forming a float or scum blanket, as the clarified liquid moves
radically downward to the outlet baffle. The treated water flows under
the outlet baffle (6), up through exit plenum and over the flow
equalizing launder weir.
The treated water flows over the launder ring, to
the overflow weir, and then to the clear well (7). A predetermined
portion of the treated water is recycled and the remainder gravity
flows to the industrial drain or to further treatment (11).
A portion of the treated water is utilized to
provide the media to deliver the dissolved air to the DAF by pumping
into a pressure tank (8) with compressed air at 75 psig. Drawing air
into a pump suction is not recommended by HEI because the inherent pump
cavitation dramatically shortens the life of the high pressure
centrifugal pump. The liquid level in the pressure tank is controlled
by HEI’s special level control that vents all undissolved air (large
bubbles) to prevent their entering the DAF separation chamber. The
pressurized water and compressed air are mixed and held long enough to
create a saturated solution. The saturated recycle water passed through
HEI’s unique pressure reduction valve (9) as it enters the mixing tube.
When the pressure is relived, the saturated solution becomes
super-saturated and the air begins to precipitate from solution.
Materials of Construction |
HEI’s standard material of construction is ¼" A36
steel plate, sand-blasted to a SPC-6 finish and coated with immersion
grade acid resistant epoxy paint. Stainless steel may be substituted as
an option. A NEMA 12 central control panel is provided to control the
entire operation.
|
|
-
Oilfield Produced Water
-
Oil Refinery
-
Paint Manufacture
-
Power Plants
-
Pulp and Paper
-
Railroad Maintenance
-
Rendering Plants
-
Seafood Processors
-
Tank Truck Cleaning
-
Tanning
-
Textile Manufacture
|
|
HEI will provide the entire turn-key DAF system to
include engineering, lift station, chemical conditioning, solids
compaction, installation and start-up. HEI engineers and manufactures
its own equipment and will provide individual items of equipment for
complete turn-key plants. |